Even as the semiconductor industry hopes to find and recruit skilled workers, a lack of talent could undermine national objectives, push up labor costs, and hinder the returns from the billions of dollars being spent, according to a McKinsey & Co report.

With government money to spur them on, the semiconductor industry in the US is forging ahead with dozens of projects to expand domestic manufacturing.
But there's a big problem: not enough labor to staff those new or upgraded facilities once they're completed, according to a new report from professional service firm McKinsey & Co. The talent needed to meet the surge in chip demand, which is particularly acute because of artificial intelligence (AI) adoption, spans three distinct labor pools - construction craft laborers, engineers, and technicians.
"Despite industry groups' efforts to raise awareness and boost recruitment, the supply remains inadequate and staffing shortages could put domestic objectives for the industry at-risk, drive-up labor costs, and delay or diminish the return on this monumental investment," McKinsey said in its report.
The CHIPS & Science Act (now called The CHIPS for America Act) passed by Congress in July 2022 set aside more than$52 billion in government incentives to spur semiconductor development and production on US soil. In addition to those investments, semiconductor companies have announced more than$200 billion in US fab investment through 2032.
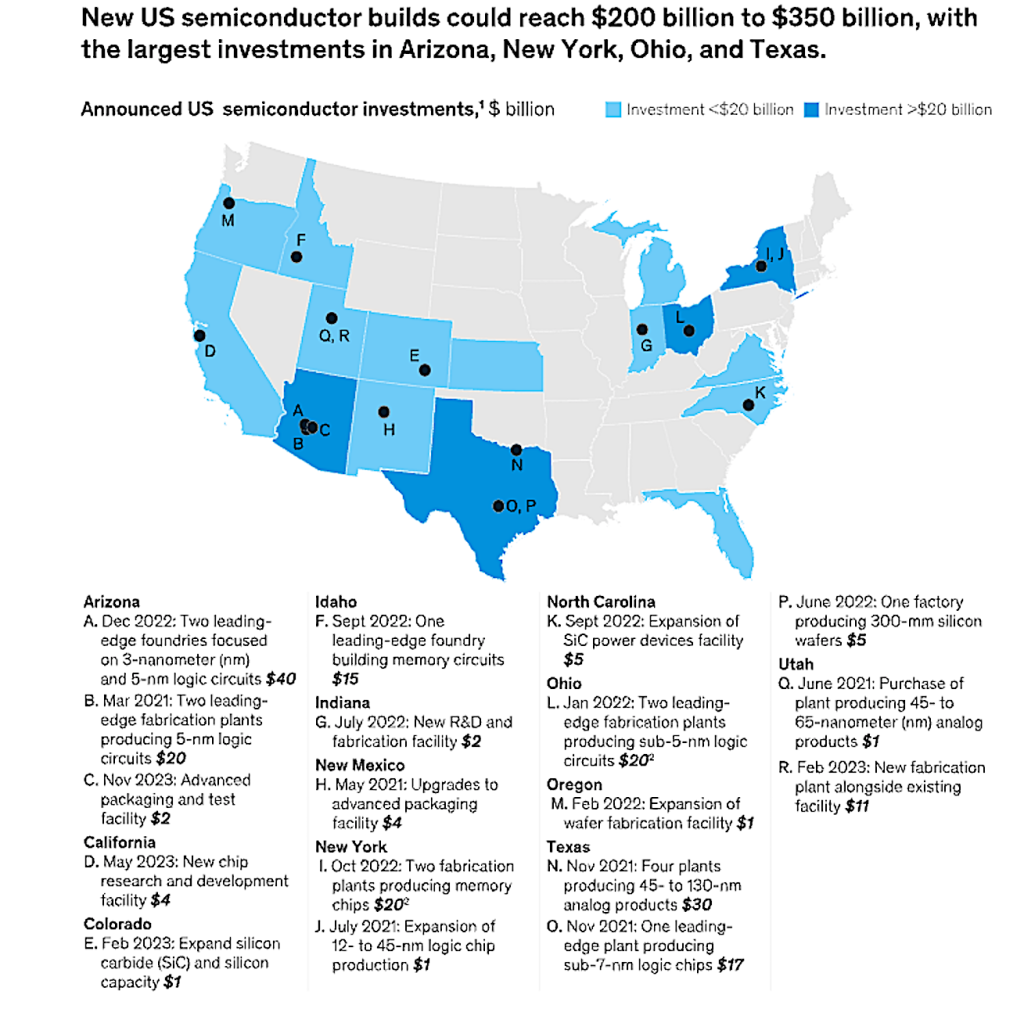
McKinsey & Co.
New builds or fab plant expansions are planned in 16 states. For example, McKinsey's analysis of company data shows that approximately 10,000 new job openings will be created through expanded operations in New York, with another 7,500 or so jobs created by four new fab builds in Arizona.
Industry analysts say the CHIPS Act is having its desired effect - the largest semiconductor designers and makers are investing in the US. By 2030, research firm IDC expects that 30% of the leading-edge chip technology will be produced in the US, Western Europe, and Japan.
For example, at the beginning of 2023, TSMC, the world's largest chip maker, began construction on a third chip fabrication plant near Phoenix, AZ. TSMC's three Arizona plants have represented flagship projects for the CHIPS Act. The TSMC project stalled, however, and the company announced it had pushed back its completion date to 2025 due to problems finding skilled labor.
It takes two to three years of construction, a year or more for equipment installation and ramp-up, and more than$20 billion to build some leading-edge facilities, according to McKinsey. And each phase involved in getting a fab up and running requires different types of talent in varying numbers. Construction craft laborers are essential to the building phase, while engineers and technicians are required to design and set up equipment and process lines during the final phases of construction.
Once operations are under way, engineers and technicians are needed to fill roles in several areas: manufacturing, integration and yield, central labs, facilities, quality assurance, product management, industrial engineering, and more. A leading-edge fab with a capacity of 20,000 to 45,000 wafers per month, for example, would employ between 1,100 and 1,350 engineers and about 950 to 1,200 technicians.
While construction of plants could be affected by manual labor shortages, the bigger question is, once fabs are built, "will there be enough technicians and engineers?" said Gaurav Gupta, a vice president analyst at Gartner Research. The decline in chip manufacturing on US shores over the past four decades has led to a lack of interest by college students to enter the field, he said.
"Intel, TSMC, and Samsung are all partnering with universities and community colleges, and once there are job openings and students see, things will improve," Gupta said. "I was recently at a conference where one of the topics being discussed was on talent and part of the reason chip firms don't attract that is they don't advertise it properly."
A potentially bigger long-term problem, however, is that as a new generation of students and workers enters the semiconductor industry, they will have different priorities - and chipmakers will need to adjust to stay competitive for talent, according to Gupta.
The US semiconductor industry needs to offer more attractive compensation packages to attract and retain talent, according to Galen Zeng, a semiconductor senior research manager with IDC in Taiwan. The industry must also implement policies that promote work-life balance to attract younger generations of workers.
The US government also needs to reform immigration policies to attract skilled labor from abroad; it could, for instance, simplify visa processes and provide tax incentives to attract talent from overseas, he said.
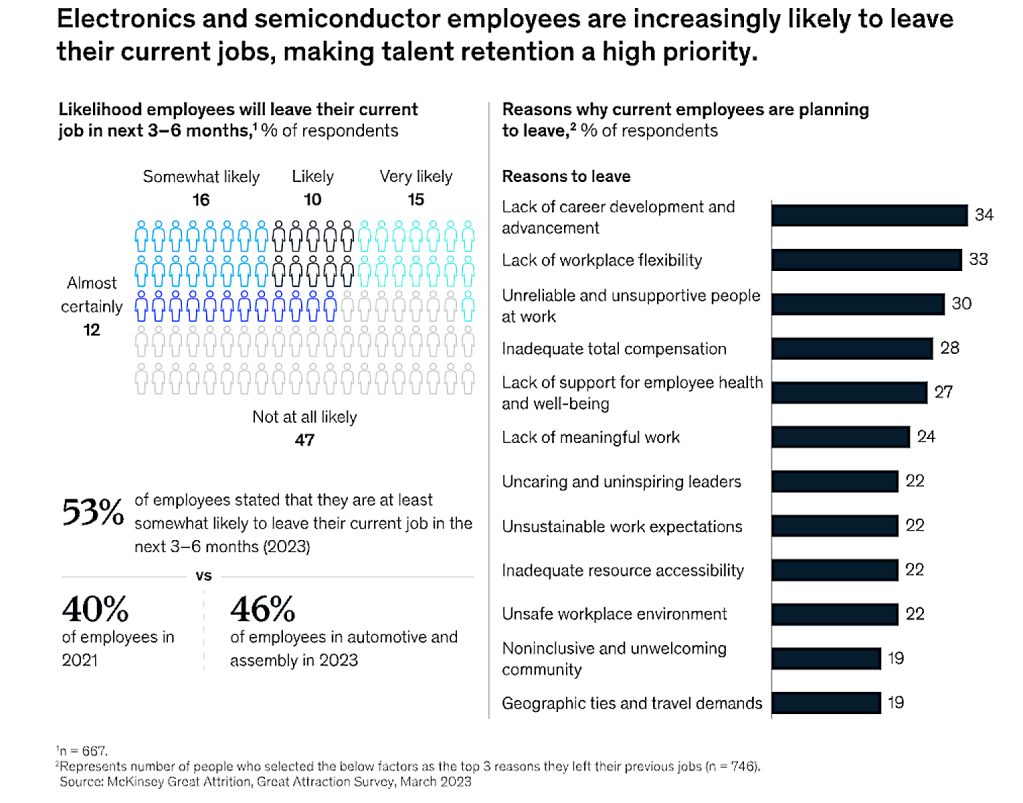
McKinsey & Co.
In recent years, it has taken longer to attract and hire semiconductor talen, according to McKinsey & Co. data. From 2018 through 2022, it took a week longer to find and hire semiconductor technologists compared to the previous seven years. In 2022, the active status of technician job postings rose to 28 days, a peak level reached prior to the start of the COVID-19 pandemic.
"At the same time, [semiconductor employee] attrition has been exceptionally high, and ... it could rise even higher," the study said.
In 2023, for example, more than half (53%) of electronics and semiconductor workers indicated they were at least somewhat likely to leave their current jobs within the next three to six months, up from 40% who said that in 2021.
The labor shortage is also not isolated to the US. Japan, South Korea, Taiwan, and Europe all face the same issue. "Addressing the talent shortage in the semiconductor industry requires a comprehensive approach, including education, policies, industry collaboration, and compensation, to ensure the long-term sustainable growth and competitiveness of the semiconductor industry in various countries," Zeng said.
Additional steps, Zeng said, that the US and other nations can take to address the problem include:
- More Science, Technology, Engineering, Mathematics (STEM) programs in education at all levels, with a foundation in semiconductors, including using semiconductor equipment to enable hands-on experience in schools.
- Training institutions that collaborate with the semiconductor industry to develop specific programs to ensure the workforce has the necessary skills for semiconductor manufacturing.
- Continuous learning for the semiconductor labor force so workers can adapt to new technologies and add longevity to careers.
- New apprenticeship programs that combine classroom instruction with on-the-job training to build strong relationships between the workforce and students.
Even under optimistic projections, there will be considerable shortfalls in the US semiconductor workforce, according to McKinsey & Co., which explored the scope of semiconductor investment and existing talent challenges, the labor pools required to operate and build fabs, and the workforce development programs in the public and private sectors to bridge the gap.
US Secretary of Commerce Gina Raimondo has recognized the US needs to double the semiconductor workforce overall, triple the number of graduates in semiconductor-related fields, and train 100,000 new technicians.
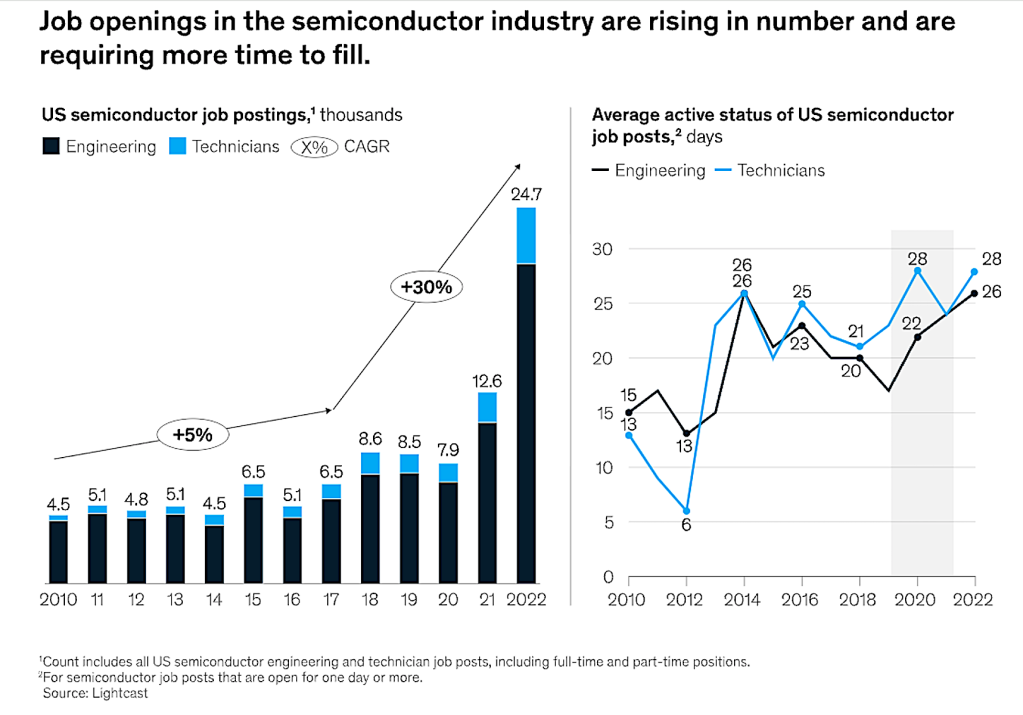
McKinsey & Co.
"CHIPS for America will embrace a whole-of-society approach across government, education, labor unions, industry and community organizations to achieve these ambitious goals," the department said in an email reply toComputerworld.
In November, the Commerce Department, which administers the CHIPS Act program, released a report on the impact of initiatives under way to build a US labor workforce for the semiconductor industry. As part of the report, the National Institute for Standards and Technology (NIST) outlined three key government initiatives, including:
- CHIPS Act incentives awards for commercial facilities to include dedicated funds for workforce development.
- $500 million for public/private workforce investments in facilities
- New commitments from chip manufacturers, states, and local governments to include registered apprenticeships and pre-apprenticeships.
"After we get CHIPS incentives out the door, CHIPS for America staff expect to work closely with incentives recipients and regional education and training partners to support implementation of workforce strategies," the Commerce Department said.
State and municipal governments are already stepping up to support the CHIPS for America workforce initiatives, with at least seven states dedicating new funding to support workforce training for semiconductor jobs, the department said. Additionally, more than 50 community colleges across 19 states have announced new or expanded programming to support semiconductor opportunities.
Increasing the local pool of US engineers will require investment by the federal government in the university and research ecosystem. A much faster solution would see the US government come to terms with the need to relax immigration laws to allow for more highly skilled foreigners from locations like Taiwan, South Korea or Japan, to help ramp up production in those new fabs, according to Josep Bori, a research director at data analytics and consulting company GlobalData.
"The alternative would be to delay such investments, but still it is not clear that universities would ramp up provision of relevant degrees without the actual demand already in place," Bori said.
According to McKinsey, US manufacturing semiconductor capacity increases are expected to create up to 48,000 jobs at fabrication plants in the next two to three years. But those new job numbers do not account for the rise in attrition the industry is likely to experience in the same time frame. In 2023, 53% of electronics and semiconductor employees indicated they were at least somewhat likely to leave their current jobs within the next three to six months, the study showed.
Workforce development programs are likely to add around 12,000 engineers and 31,500 technicians by 2029, according to McKinsey. "Nevertheless, even when these are combined with CHIPS Act efforts, optimistic projections indicate there will still be considerable shortfalls in the workforce," it said.
GlobalFoundries, which in February was awarded$1.5 billion in CHIPS Act money to help it expand and create new US manufacturing capacity and capabilities, said it has a number of initiatives in place to tackle the workforce shortage. Earlier this month, the company announced a student loan reimbursement program.
Among other efforts, including a military veteran's outreach effort, GlobalFoundries launched technician internship programs offering hands-on paid experience to students while they're enrolled in community college programs. "We hire graduates of two-year degrees into Maintenance Technician roles," a spokesman said.